Are you looking to streamline your logistics operations? Look only as far as Singapore’s premier distribution center. Boost efficiency and cut costs today. Contact us!
distribution center definition
A distribution center is a strategically located facility within the supply chain that serves as a hub for receiving, storing, and distributing goods to retailers, wholesalers, or directly to consumers. These centers play a critical role in logistics, efficiently managing inventory, order fulfillment, and transportation activities. Distribution centers are designed to streamline the movement of products, optimize stock levels, and enhance the overall efficiency of the supply chain. With advanced technologies and logistics expertise, these centers ensure timely and accurate distribution, contributing to the seamless flow of goods from manufacturers to end-users.
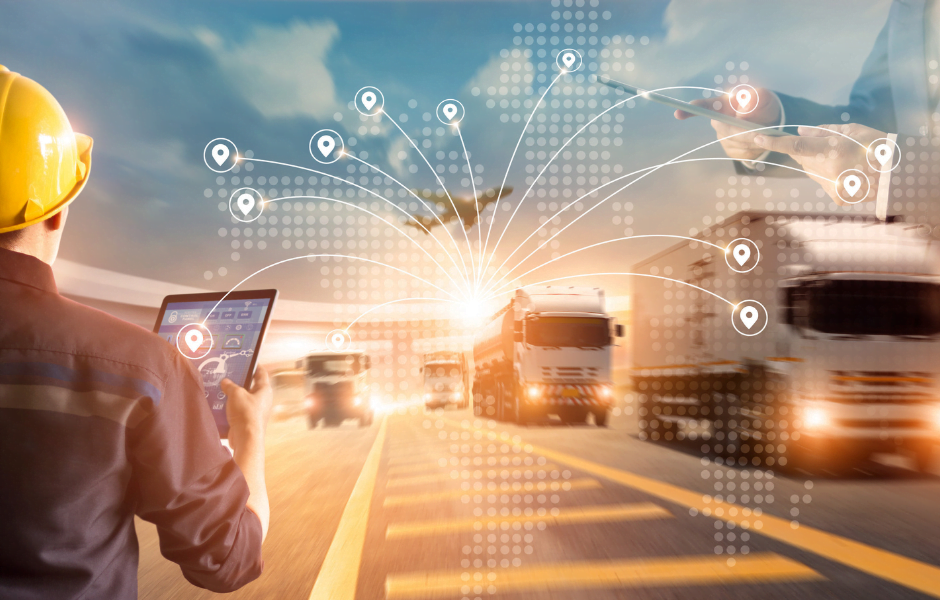
Distribution Centers: Streamlining Your Logistics
Distribution centers are vital in streamlining logistics and optimising the supply chain for businesses. They are designed to improve efficiency, reduce costs, and ensure customer satisfaction. In this article, we will discuss the benefits of distribution centers, the critical processes involved, the technology and tools used, and how they can help you optimise your supply chain costs.
Benefits and Key Processes Explained: Boosting Efficiency and Customer Satisfaction
There are strategically located facilities that act as intermediaries between manufacturers and retailers. They streamline logistics by receiving, storing, and redistributing products to customers. This allows businesses to reduce lead times, lower inventory levels, and respond quickly to changing customer demands.
Key processes involved in these centers include receiving, putaway, order picking, packing, and shipping. These processes are streamlined to ensure maximum efficiency and accuracy, boosting customer satisfaction. By utilising a distribution center, businesses can improve their speed of delivery, reduce errors and damages, and provide better inventory visibility.
How They Work: Maximising Operations for Your Business
Distribution centers receive products from manufacturers or suppliers and store them in designated areas. Once an order is received, the products are picked, packed, and shipped to the customer. The entire process is managed using a warehouse management system that automates tasks, tracks inventory, and optimizes workflow.
They also offer value-added services such as kitting, labelling, and customisation. This allows businesses to differentiate their products and add value to their customers. Moreover, distribution centers can handle returns, repairs, and refurbishment, reducing business workload and improving customer satisfaction.
Technology and Tools: Innovating Logistics with Technology
Distribution centers use advanced technology and tools to optimize their operations. These include warehouse management systems, inventory tracking software, automated storage and retrieval systems, and material handling equipment. These tools enable businesses to manage inventory more efficiently, reduce labor costs, and improve accuracy.
Moreover, they are increasingly adopting new technologies such as robotics, AI, and IoT to enhance their capabilities further. For example, robots can be used for picking and packing, reducing human errors and increasing efficiency. IoT sensors can track inventory in real time, improving visibility and reducing waste.
Costs: Optimizing’s Your Supply Chain Costs
One of the critical benefits of distribution centers is that they help businesses optimize their supply chain costs. By consolidating products in a central location, companies can reduce transportation costs, lower inventory carrying costs, and minimize the risk of stockouts. Moreover, they can help businesses avoid the need for expensive warehousing and logistics infrastructure, allowing them to focus on their core competencies.
Warehouse vs Distribution Center: Which One Fits Your Business?
The difference between warehouses and distribution centers is that warehouses are used for long-term storage. Incorporating distribution centers into your logistical operations can yield a cornucopia of benefits. These vast warehouses provide ample space for storage in addition to a myriad of fulfilment and distribution services. Think product mixing, packaging, and cross-docking – to name a few! With their multipurpose functionality, it’s no wonder that businesses are jumping on the distribution center bandwagon. Consider implementing a distribution centre if you want to enhance your logistical strategy.
Differences Explained: Understanding the Key Features of Each
Warehouses and distribution centers may seem similar at first glance, but the two have significant differences. Warehouses are storage facilities designed for the long-term storage of goods. They are often used for products with low turnover rates, such as raw materials or finished goods waiting for delivery. On the other hand, they are designed for short-term storage of goods ready for delivery. They are strategically located near transportation hubs and are designed to streamline logistics.
Types of Storage Used: Choosing the Right Storage for Your Needs
Warehouses typically use static storage methods, such as pallet racking or bulk storage. These methods are ideal for products that are not frequently accessed and require much space. On the other hand, distribution centers use dynamic storage methods, such as flow-through racking or pick modules. These methods are designed to optimize the movement of goods, reducing the time it takes to get products from storage to delivery.
Benefits and Drawbacks: Weighing the Pros and Cons
One of the main benefits of using a warehouse is that it provides long-term storage for goods that are not frequently accessed. Additionally, warehouses often have lower rental rates than distribution centers, making them a more affordable option for businesses. However, warehouses may not be suitable for companies with high inventory turnover rates or requiring fast delivery times.
On the other hand, they offer a range of benefits for businesses, including faster delivery times, reduced transportation costs, and improved customer satisfaction. They are designed to optimize the logistics process, ensuring that products are delivered quickly and efficiently. However, distribution centers may be more expensive than warehouses, and businesses may need to pay for additional value-added services.
Why Companies Use Distribution Centers: The Importance of Logistics Centers
In today’s fast-paced business world, the importance of efficient logistics and supply chain management cannot be overstated. They are critical in optimizing logistics operations, improving efficiency, and enhancing customer satisfaction. In this article, we will explore the importance of distribution centers in enhancing your supply chain and increasing your business efficiency.
Importance of Distribution Centers: Enhancing Your Supply Chain
Distribution centers are an essential part of modern supply chains, providing a centralized location for storing and distributing goods. They are strategically located near transportation hubs and are designed to streamline logistics. Businesses can reduce transportation costs, improve lead times, and increase inventory visibility by using a distribution centre.
One of the main benefits of using a distribution center is managing inventory more efficiently. Distribution centers allow businesses to store products closer to their customers, reducing the time it takes to get products from storage to delivery. This results in faster delivery times, improved customer satisfaction, and a competitive advantage in the market.
Role in Supply Chain Management: Increasing Your Business Efficiency
Distribution centers are critical in supply chain management, providing services that increase business efficiency. They can handle various tasks, including inventory management, order fulfilment, and transportation. By outsourcing these tasks to a distribution center, businesses can focus on their core competencies and achieve greater efficiency.
Distribution centers also provide value-added services that can help businesses increase revenue and customer satisfaction. For example, they can give kitting and assembly services, allowing companies to customise products for their customers. They can also provide labelling and packaging services, ensuring products are delivered professionally and on time.
Distribution Center Processes: Managing Your Operations with Precision
Distribution centers play a vital role in the supply chain by managing the movement of goods from suppliers to customers. To achieve maximum efficiency, distribution centers must execute their operations precisely. This article will explore the critical processes of managing a distribution center, including receiving and inspecting goods, inventory management and tracking, order fulfilment and shipping, returns management, and reverse logistics.
Receiving and Inspecting Goods: Ensuring the Quality of Your Products
Receiving and inspecting goods is the first step in the distribution center process. It involves checking the quality and quantity of goods from suppliers. This process ensures that any damaged or defective items are identified and returned to the supplier. Logistic companies has a team of experts trained to handle and inspect all types of goods. They use advanced technology to track and monitor inventory, ensuring that all goods are received and reviewed precisely.
Inventory Management and Tracking: Keeping Your Inventory Organized and Up-to-Date
Inventory management and tracking are critical to the success of any distribution center. It involves organizing and tracking inventory to ensure products are available when customers need them. Logistic compnies uses advanced inventory management systems to track and monitor inventory levels in real time. They also offer customized inventory solutions to meet the specific needs of each business, ensuring that inventory is always organized and up-to-date.
Order Fulfilment and Shipping: Delivering Your Products to Your Customers
Order fulfilment and shipping are the final stages of the distribution center process. It involves picking, packing, and shipping products to customers promptly and efficiently. Logistic companies offer a range of shipping options to meet the needs of each business. They use advanced technology to optimize shipping routes and reduce delivery times, ensuring that products are delivered to customers as quickly and efficiently as possible.
Returns Management and Reverse Logistics: Handling Returns and Exchanges
Returns management and reverse logistics are essential parts of the distribution center process. It involves handling customer returns and exchanges and ensuring that products are returned to inventory or the supplier as needed. Howely.com.sg has a dedicated team of experts trained to handle returns and exchanges efficiently. They also offer reverse logistics solutions that help businesses manage the flow of goods back through the supply chain.